

The parts are core elements of the sheet-fed offset presses that Heidelberger Druckmaschinen AG, as the market leader, provides to users in the print media industry worldwide. It acts as a center of excellence for the manufacture of castings, such as printing press side panels or cylinders, for the entire Heidelberg Group, which has a yearly revenue of three billion euros (~$4.4 billion) and 15,000 employees. The Amstetten factory is one of the most up-to-date and efficient foundries in all of Europe. This enables them to predict precisely what the quality and characteristics of the cast iron cylinder will be, when it leaves the mold and is finally integrated in a Heidelberg printing press. They ran through the entire process in advance with simulation software.

The engineers of Amstetten Foundry, which forms part of Heidelberger Druckmaschinen AG, are familiar with every detail of the casting system. The movement of the flowing metal in the casting rigging and in the gradually filling mold for printing press cylinders and the subsequent solidification process are only chaotic and accidental, at first glance.
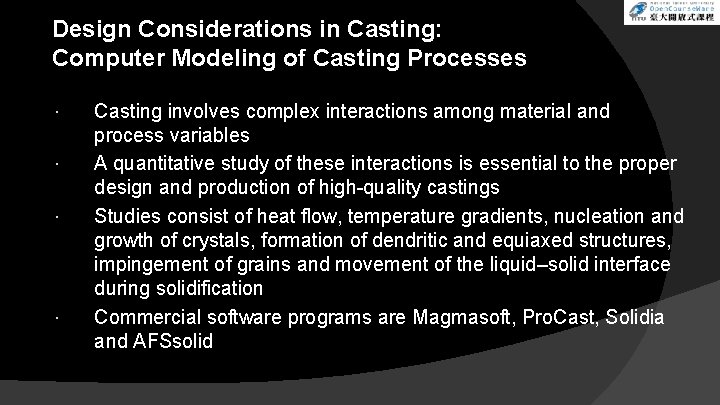
The 1400 ☌ hot cast iron melt gushes through the gate into the mold. Simulation in action: casting quality, realizing innovation, reducing costs
